Revolutionizing CMM Inspection at Savage Precision
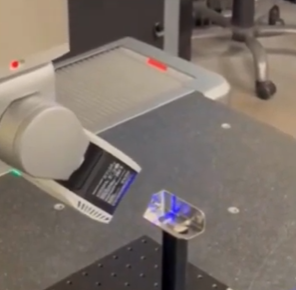
How Our New Laser Head Attachment Enhances Machine Shop Quality Control
At Savage Precision, machine shop quality control is a top priority. That’s why we recently invested in an advanced laser head attachment for our coordinate measurement machine (CMM), an investment that is already transforming our inspection processes. By replacing traditional probe-based measuring with high-speed laser scanning, we’re improving precision, efficiency, and data collection, and passing the time savings on to our customers.
Why Savage Precision Invested in Laser Scanning Technology
For decades, manufacturers have relied on CMM inspection using mechanical probes to verify part dimensions. While effective, this method is time-consuming and limited in capturing complex surfaces. The addition of a laser head attachment changes everything.
One of the key motivators behind this $70,000 investment was the need to accurately replicate F-16 tooling for Lockheed Martin. The original F-16 tooling, designed in the 1970s, features intricate contours, curves, and joggles that a traditional probe cannot effectively capture. With the laser scanner, we can now scan the tooling, extract precise coordinates and accurate measurements, and create perfect replicas, something previously impossible with a mechanical probe.
The laser head attachment also measures five times faster than a traditional probe, reducing inspection time and allowing us to verify parts at multiple stages of production with unprecedented speed.
How This Precision Measurement Technology Transforms the CMM Inspection Process
Unlike traditional probes that require physical contact with a part, the laser scanning system captures data in seconds, mapping out the entire surface with pinpoint accuracy. This upgrade allows us to:
- Inspect parts at any stage of production, from first operation to final verification.
- Reverse-engineer parts quickly and accurately for reproduction or modification.
- Reduce human error and manual data entry, streamlining quality control processes.
- Drastically reduce inspection times. Verifications that once took over an hour can now be completed in minutes.
- Deliver enhanced accuracy and repeatability, ensuring that each part meets precise specifications.
Before this investment, first article inspections were often slowed down by the time it took to manually check every dimension and record the data. Now, the laser scanner captures all measurements instantly, allowing our inspectors to simply sign off on a scanned record, saving valuable time and reducing paperwork.
A Game-Changer for Clips and Brackets
While this technology benefits all areas of production, it’s particularly transformative for inspecting clips and brackets, two of Savage Precision’s most commonly produced parts.
Before the laser head attachment, a Raytheon diode part inspection took 1 hour and 15 minutes using a probe. Now, the same process takes just 10 minutes with laser scanning. This efficiency means we can inspect more parts in less time, reducing bottlenecks and ensuring that every product meets the highest quality standards before leaving our facility.
Speed, Accuracy, and Data Precision
Beyond speed, the laser head attachment also offers unparalleled precision measurement technology. It’s capable of detecting even the smallest imperfections, down to the bumps in the double-sided tape used to hold parts in place during inspection. This level of detail ensures our parts are manufactured with extreme accuracy, meeting the strictest industry standards.
By cutting down on manual processes and allowing for real-time scanning at multiple production stages, the laser head attachment has already improved overall workflow, reducing setup times and increasing output efficiency.
The Future of Precision Measurement at Savage Precision
With this new coordinate measurement machine enhancement, Savage Precision is continuing its mission of continuous improvement in machine shop quality control. The laser head attachment represents our commitment to faster, more accurate, and more efficient manufacturing.
By integrating the latest precision measurement technology, we are not only improving our internal processes but also enhancing the quality and reliability of the products we deliver to our clients. As we move forward, this investment will allow us to expand our capabilities, take on more complex projects, and continue exceeding industry standards. Contact us today to learn how our advanced CMM inspection technology can support your next project.